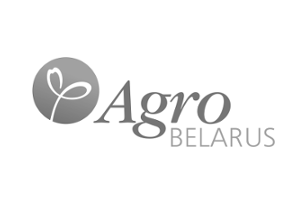
Как изменилась работа автопарка и ферм УП «Дружбинец» после автоматизации с RESURSCONTROL
28.08.2025
Сушка – это сложный процесс тепло- и массообмена. В то же время это технологический процесс, при проведении которого должны быть сохранены не только исходные свойства материалов, но, в ряде случаев, даже улучшены.
С целью обеспечения продовольственной безопасности страны, в соответствии с государственной программой возрождения и развития села планируется довести урожай зерновых до 10 млн.т. Наряду с этим увеличивается и производительность выпускаемых зерносушильных комплексов. Однако их производительность не всегда пропорциональна энергопотреблению. Например, СЗК-10Г (производительность по сырому зерну при снижении влажности с 20 до 14% ,10 т/ч), имеет установленную мощность электродвигателей 40,4кВт, теплогенератора 0,8МВт. А зерносушильный комплекс марки ЗСК-40Г с производительностью 40 т/ч, мощность теплогенератора 4 МВт, но удельный расход электроэнергии при этом 250 кВт.
В процессе переработки зерновых культур около 70% энергии расходуется на сушку и очистку зерна. Потребляемая мощность отечественных комплексов на порядок выше зарубежных аналогов. В связи с этим существует актуальный вопрос: как достичь снижения энергозатрат?
Прежде всего, активно проводится работа по снижению энергозатрат ЗСК на основе оптимизации энергетических процессов. С этой целью разработана методика проведения исследований режимов работы различных типов ЗСК. В частности, проводится сбор первичной информации на основе энергетических аудитов ЗСК, обработка результатов и анализ энергоэкономических показателей. Одновременно предусматривается разработка энергетических балансов ЗСК с их последующей оптимизацией.
Стоит задача в необходимости многопланового анализа и обоснования различных способов энергообеспечения зерноочистительно-сушильных комплексов, а также оптимизация режимов энергопотребления с целью снижения расходов энергоресурсов.
Например, установлено, что КПД зерносушилки представлено зависимостью:
где: t0-температура наружного воздуха;
t1 -температура воздуха на входе в сушилку;
t2 -температура воздуха на выходе из сушилки;
Суммарный расход теплоты ΣQ (Кдж/ч) в зерносушилке можно представить следующим выражением:
ΣQ=Q1+ Q2+ Q3+ Q4+ Q5+ Q5,
где Q1 – затраты теплоты на испарение влаги;
Q2 – потери теплоты на нагрев зерна;
Q3 – потери теплоты с отходящими газами ( с отработавшим агентом сушки);
Q4 – потери в окружающую среду ( через нагретые поверхности);
Q5 – потери теплоты на нагрев транспортных средств;
Q6 – потери теплоты в следствии неполного сгорания топлива (от химического и механического недожога).
Удельные значения составляющих данного выражения представлены в табл.1.
Удельная доля затрат и потерь теплоты (%) на сушку в зерносушилке.
Статьи теплового баланса |
Доля теплоты | |
от общей суммы затрат и потерь |
от непроиз-водительных потерь | |
1.Затраты на испарение влаги (термический КПД) |
53,2 |
— |
2. Потери теплоты на нагрев зерна |
15 |
32 |
3. Потери теплоты с отработавшим агентом сушки |
23,9 |
51,1 |
4. Потери теплоты в окружающую среду |
6,9 |
14,7 |
5. Потери теплоты на химический и механический недожог |
1 |
2,2 |
Итого: затрат и потерь потерь |
100 46,8 |
— 100 |
Анализ данных показывает, что для увеличения ŋс (КПД сушки) необходимо увеличить долю затрат теплоты на испарение влаги Q1. Наибольшее значение потерь имеют потери теплоты с отработавшим агентом сушки Q3 51,1% всех потерь.
В качестве примера можно привести результаты изучения опыта использования ЗСК-40Г на предприятии ОАО «Октябрьская революция». В таблице 2 приведены значения температур нагретого, отработанного теплоносителя и в 1-ой секции каждой из шахт зерносушилки за период сушки партии фуражного ячменя в ночную смену.
Таблица – 2. Значения температур в различных зонах зерносушилки.
Время изм. |
Темп. нар. воздуха t0 |
Температура. нагретого теплоносителя. t1 |
Температура. отработанного теплоносителя. t2 |
Разница температур | |||
t, мин. |
0C |
1-й0C |
2-й0C |
1-я0C |
2-я0C |
1-я0C |
2-я0C |
22,00 |
14 |
91 |
84 |
33 |
33 |
19 |
19 |
22,15 |
14 |
91 |
85 |
35 |
35 |
21 |
21 |
22,30 |
14 |
84 |
78 |
35 |
35 |
21 |
21 |
22,45 |
14 |
92 |
85 |
36 |
36 |
22 |
22 |
23,00 |
14 |
92 |
85 |
37 |
37 |
23 |
23 |
23,15 |
14 |
88 |
81 |
37 |
37 |
23 |
23 |
23,30 |
13 |
65 |
85 |
38 |
35 |
25 |
22 |
23,45 |
13 |
93 |
85 |
37 |
34 |
24 |
21 |
00,00 |
13 |
77 |
70 |
37 |
35 |
24 |
22 |
00,15 |
12 |
83 |
77 |
36 |
36 |
24 |
24 |
00,30 |
12 |
86 |
80 |
37 |
35 |
25 |
23 |
00,45 |
12 |
38 |
31 |
38 |
36 |
26 |
24 |
1,00 |
12 |
18 |
18 |
36 |
34 |
24 |
22 |
1,15 |
12 |
15 |
15 |
33 |
31 |
21 |
19 |
1,30 |
12 |
98 |
91 |
29 |
29 |
17 |
17 |
1,45 |
12 |
95 |
89 |
37 |
27 |
25 |
15 |
2,00 |
12 |
93 |
86 |
31 |
31 |
19 |
19 |
2,15 |
12 |
94 |
86 |
35 |
33 |
23 |
21 |
2,30 |
12 |
93 |
86 |
38 |
35 |
26 |
23 |
2,45 |
12 |
93 |
85 |
41 |
35 |
29 |
23 |
3,00 |
12 |
93 |
86 |
43 |
35 |
31 |
23 |
3,15 |
12 |
94 |
85 |
44 |
34 |
32 |
22 |
3,30 |
12 |
74 |
67 |
42 |
34 |
30 |
22 |
3,45 |
12 |
25 |
25 |
38 |
32 |
26 |
20 |
итого ср: |
12,6 |
77,7 |
72,7 |
36,8 |
33,9 |
24,1 |
21,3 |
Из таблицы видно, что при среднем значении температуры наружного воздуха за период сушки в 12,6 0С температура отработанного теплоносителя составляет 36,8 и 33,9 0С соответственно. Для уменьшения этих потерь целесообразно использовать рекуперацию тепла отработавших газов. Возможен вариант использования теплоутилизатора.
Известно, что современные теплообменники имеют КПД 60% и более, а использование отработавшего сушильного агента напрямую нерационально из-за его переувлажнения.
Проанализировав полученные данные, предлагается использовать схему рекуперации приведенную на рис.1, взамен существующей.
Оптимизацию же процесса сушки целесообразно проводить не по отдельным более или менее значимым параметрам, а в комплексе. Только полные и всесторонние исследования позволят наилучшим образом смоделировать процесс сушки c последующей оптимизацией.
В целях повышения энергоэффективности отечественных зерносушильных комплексов, мы и в дальнейшем намерены проводить анализ различных способов энергоснабжения ЗСК, разработку методов оптимизации энергопотребления, находить экономическое обоснование и разрабатывать агротехнические требования, а также обосновывать рациональные способы энергообеспечения и энергопотребления ЗСК. Это позволит снизить энергоемкость производства зерна не менее чем на 15-20%.
П. Климкович,
магистр технических наук.
Белорусский государственный аграрный
технический университет.
г. Минск
Из доклада на международной научно-технической конференции «Энергосбережение – важнейшее условие инновационного развития АПК».
г. Минск.
Россия и СНГ 03.09.2025
Новости компаний 01.09.2025
Новости компаний 22.04.2025
Новости компаний 02.03.2025
Новости компаний 08.08.2022
Животноводство 05.02.2025
Животноводство 27.01.2025
Животноводство 10.10.2024
Животноводство 18.11.2021
Животноводство 17.05.2021
Чтобы оставить комментарий или выставить рейтинг, нужно Войти или Зарегистрироваться