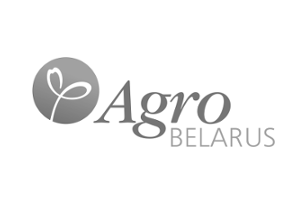
«Я не очень разговорчив с людьми и более разговорчив с растениями», – успешный садовник о цветах, любви и наболевшем
02.10.2017
Российское станкостроение сегодня стало забытой отраслью. Об этом говорят сами участники отрасли, справедливо замечая, что если мы хотим модернизировать страну, то надо начинать с возрождения станкостроения. Это одна из тех системообразующих отраслей, которые составляют основу технологической безопасности страны. И возможности для ее возрождения есть: многие из выживших предприятий сохранили потенциал роста.
Это не пустые слова. Простой пример и малоизвестный факт: для восстановления оборудования на Саяно-Шушенской ГЭС после аварии в 2009 году компании «Силовые машины» понадобилось модернизировать тяжелый карусельный станок, выпущенный немецкой фирмой Schiess в 1937 году, для изготовления на нем крупногабаритных деталей гидротурбин. Тендер выиграло ООО «Киров-Станкомаш» - дочернее общество ОАО «Кировский завод» (Санкт-Петербург). Задача была не из простых: только планшайба станка имеет в диаметре 14 м и весит 400 тонн. В ноябре 2011 г. заказ был успешно выполнен. При этом станку были не только возвращены характеристики, заложенные при изготовлении 75 лет назад, но и «осовременены» управление, приводы, гидравлика, расширены функциональные возможности. Примечательно, что сложнейшая работа по глубокой модернизации уникального оборудования, которое в настоящее время практически не выпускается, была выполнена предприятием, созданным всего 8 лет назад.
О сегодняшнем состоянии российского станкостроения и перспективах его развития рассказал директор ООО «Киров-Станкомаш» Егор Скрипкин.
- Каковы тенденции развития современного рынка станкостроения?
- Прежде чем говорить о тенденциях, стоит вкратце напомнить постсоветскую историю отечественного станкостроения. Наиболее показательные примеры можно привести по нашему региону. В советское время Петербург, тогда Ленинград, был одним из центров этой отрасли. К сожалению, с развалом СССР за прошедшие два десятилетия от этого сектора промышленности города мало что осталось. Настолько жестким катком прошелся по нему развал страны, что из сотни крупнейших заводов, организаций и учреждений, которые формировали станкоинструментальную отрасль страны, осталось всего полтора десятка. Только единицы из них сохранили статус предприятий полного цикла. Если раньше здесь были огромные комплексы, которые обеспечивали весь «передел», начиная от литья, продолжая механической обработкой деталей и узлов и заканчивая сборкой и финишными операциями, то теперь выжившие предприятия преимущественно имеют узкую специализацию или занимаются ремонтом и модернизацией оборудования, выпущенного ранее.
- А с чем связан развал отрасли? Прекратился спрос на станки?
- Безусловно, в первую очередь, прекратился спрос. Во времена СССР была глобальная плановая система, которая распределяла заказы на производство оборудования по огромному количеству заводов. Станкостроительные предприятия имели плановые задания по выпуску сотен и тысяч единиц продукции. Советский Союз в доперестроечные годы находился на лидирующих позициях по производству металлообрабатывающего оборудования. В 1990 году, например, наша страна занимала по этому показателю третье место в мире. Ни одна крупная выставка не обходилась тогда без российских производителей, и оборудование зачастую раскупалось прямо на экспозициях. Как известно, эта система развалилась. Предприятия в одночасье лишились заказов и финансирования, оказались не в состоянии обеспечивать собственный полный цикл и конкурировать в новых рыночных условиях: ведь станкостроение – очень ресурсоемкое производство. В результате, по оценкам экспертов, валовый объем продукции в отрасли сейчас не превышает 5% от прежнего уровня, страна откатилась на 22-е место в мире, а ее доля в мировом производстве составляет около 0,3%. Теперь на международных выставках почти не встретишь российских производителей станочного оборудования.
В дополнение к этому существовали и проблемы технологического плана. Например, переход на цифровые системы управления кардинально изменил мировое станкостроение, а наши производители не успели вовремя перестроиться. Отчасти это связано и с тем, что в СССР серьезно отставала разработка компьютерной техники и электронных систем управления. Отечественная компонентная база тоже стала деградировать, и мы до сих пор не можем обойтись без импортных систем управления, гидравлики и многого другого. Хотя, есть и исключения. Например, российская компания Балт-Систем, специализирующаяся на разработке программного обеспечения для станочного оборудования, в некоторых проектах способна заместить импортные аналоги.
- Какова сегодняшняя ситуация и какие существуют тенденции?
- Если коротко, то сейчас основные проблемы отрасли – устаревшие технологии, потерянные производственные мощности, утраченная конструкторская школа и отсутствие квалифицированной молодых специалистов, готовых подхватить то, что удалость сохранить, и поднять на новый современный уровень. К сожалению, эта ситуация в лучшую сторону не меняется. Сегодня станкостроение находится на переломном этапе, когда уже разрушено старое, но еще не построено новое. Принятая в прошлом году федеральная программа развития станкоинструментальной промышленности до 2016 года буксует, адресных инвестиций нет, как нет и поддержки на налоговом и законодательном уровнях. Борьба за выживание совсем не оставляет ресурсов для развития, вложений в НИОКР, обучения квалифицированных кадров, поддержания конкурентоспособности своей продукции. Если государство всерьез не озаботится проблемами отрасли, то в перспективе страну ожидает полная зависимость отечественной промышленности от импортных средств производства без шансов когда-либо вернуть утраченные позиции. Получить передовые технологии других стран невозможно, и мы всегда будем на поколение, а то и больше позади.
- Как Вы оцениваете отставание от ведущих зарубежных производителей?
- По разным оценкам разрыв составляет от 30 до 40 лет.
- Но если государство все же озаботится и заработают целевые программы, можно ли исправить ситуацию? Ведь наследие прошлых времен немалое – есть площади, есть громадный станочный парк, да и спрос имеется?
- Вы правы. Станкоинструментальный рынок России – это один из немногих рынков, где спрос превышает предложение. Причем, не имея достаточных средств на приобретение нового оборудования, многие предприятия идут по пути модернизации существующих основных фондов. По данным на середину этого года, более 70% из почти полутора миллионов имеющихся в стране станков эксплуатируются свыше 20 лет (при норме в два раза меньшей) и находятся на грани полного физического износа. Поэтому о недостатке заказов, прежде всего по модернизации станочного оборудования, речи не идет. Правда, заказы все эти несерийные, каждый раз приходится сталкиваться с новыми задачами, разрабатывать новые проекты под заказчика. Кстати, в эту рыночную нишу одним из первых вошло ООО «Киров-Станкомаш». Но основная проблема станкостроения даже не в отсутствии серийных заказов или нехватке финансовых ресурсов. Гораздо важнее отсутствие в нужном количестве квалифицированных специалистов: инженеров, конструкторов, технологов, специалистов рабочих профессий. Сейчас практически нет инженерно-технических кадров среднего возраста – 35 - 45 лет. К тому же, существовавшая прежде мощная система технического вузовского образования и ПТУ во многом разрушена, да и карьера инженера существенно утратила свою привлекательность для молодежи. Поэтому многие предприятия вынуждены самостоятельно решать эту задачу: они взаимодействуют с вузами, приглашают на стажировки студентов 4-5 курсов, разрабатывают для них программы. Мы тоже проводим такую работу, но отмечаем, что молодых людей пугает длинный путь по карьерной лестнице – стать хорошим специалистом на заводе можно лишь через пять лет, а то и больше. А тех, кто приходит по призванию, слишком мало. Эту кадровую проблему, в отличие, скажем, от финансовой, в одночасье решить не удастся.
- Вы упомянули нишу, связанную с модернизацией станков. Как Вашему заводу удалось в нее войти?
- Кировский завод создал профильную станкостроительную компанию «Киров-Станкомаш» в 2004 году изначально с целью модернизации своих собственных немалых основных фондов. Потребности рынка и мощная производственная база Кировского завода создали условия для расширения этой задачи. Со временем «Киров-Станкомаш» стал одним из лидеров, прежде всего на Северо-Западе, в области высокотехнологичной модернизации металлообрабатывающего оборудования, в том числе тяжелых и уникальных станков. Первой визитной карточкой стал осуществленный в 2008 году для Ленинградского металлического завода (ОАО «Силовые Машины») проект модернизации уникального токарно-карусельного станка фирмы Schiess 1939 года выпуска. Такого проекта в России раньше не было. Уже размеры станка внушают почтение: на его планшайбе диаметром 19 м могут поместиться 1000 человек, а вес станка составляет порядка 4 тыс. тонн. В этом проекте был реализован сложный синтез всего, что есть в станкостроении: мы не просто восстановили паспортные характеристики станка, но и отчасти перекрыли их новыми функциями, а также модернизировали систему управления с применением оборудования фирмы Siemens.
А затем был еще более сложный заказ на аналогичный станок, предназначенный для изготовления новых блоков для разрушенной Саяно-Шушенской ГЭС. Кстати, именно этот заказ во многом обеспечил загрузку предприятия на пике кризиса и помог нашему станкостроительному заводу выжить.
- Расскажите, пожалуйста, с какими проблемами компания столкнулась в 2008-2010 годах и как удалось сохранить позиции в этот период?
- Станкостроение оказалось в эпицентре кризиса, прежде всего, потому что обрушилось тяжелое машиностроение – наш основной заказчик. Известно, что капитальные вложения в оборудование – строка бюджета любого предприятия, первая попадающая под сокращение при отсутствии реальной загрузки производственных мощностей. Мы пошли другим путем, сделав ставку на дополнительные финансовые вложения в бизнес и расширение сферы наших услуг. Не обошлось, конечно, без оптимизации производства по многим проектам, грамотного сокращения затрат и накладных расходов и поддержки Кировского завода. За счет этого мы не только не потеряли свои позиции, а смогли преодолеть кризисный период с минимальными потерями и быстро нарастили объемы производства.
- Какую роль сыграло тогда ваше партнерство с компанией Monforts?
- С немецкой фирмой Monforts, производящей токарные обрабатывающие центры с уникальной гидростатической направляющей, мы сотрудничаем с 2008 года. Именно в этот период мы начали концентрировать свои усилия не только на производстве и модернизации оборудования, но и на продукте более высокого порядка – технологическом инжиниринге. Мы не просто поставляем оборудование, но и обеспечиваем заказчика комплексом услуг в рамках полного технологического цикла: технологии, оборудование, инструмент, обучение и сервисное обслуживание, как гарантийное, так и послегарантийное. Другими словами, реализуем «под ключ» проект, который обеспечивает заказчику оптимальное решение технологической задачи производства продукции с наилучшим соотношением «затраты – результат». В этом случае первостепенное значение приобретает не стоимость станочного оборудования, а себестоимость продукции, изготавливаемой заказчиком, причем не только на наших станках. Мы практикуем индивидуальный, проектный подход и отвечаем за конечный результат. При этом для нас важно иметь максимально широкий выбор поставщиков оборудования для того, чтобы предложить заказчику наилучшее решение. Компания Monforts является одним из таких поставщиков и взаимодействие с ней – это один из аспектов нашей инжиниринговой деятельности. Мы в данном случае выступаем в роли дистрибьютора продукции нашего партнера. Кроме того мы являемся представителями немецкой фирмы Chiron, производящей фрезерные обрабатывающие центры. В планах компании - значительно расширить ассортиментный ряд. Основным критерием выбора производителя является качество оборудования.
- Как вы считаете, соответствует ли требованиям времени нормативная база в станкостроении?
- Насчет нормативной базы я не готов комментировать. А вот в части налогообложения у нас могли бы быть лучшие условия. Предприятию с высокой долей затрат на оплату труда в структуре себестоимости, а именно таким предприятием является «Киров-Станкомаш», очень сложно работать на рынке и конкурировать с другими компаниями. Приходится платить большие налоги, не рассчитывая на какие-либо льготы и преференции. А ведь во многих странах мира продукция или предприятия станкостроения субсидируются государством. Китай, например, предоставляет невероятные государственные льготы, субсидии, нулевые ставки по кредитам, а у нас этого в принципе нет. Возникает ощущение, что станкостроение – забытая отрасль и на нее просто не обращают внимания. В свете принятого правительством курса на модернизацию странынеобходимо начинать возрождение таких системообразующих отраслей, как станкостроение, приборостроение, производство электроники и средств автоматизации.
- Насколько сейчас востребована ваша продукция в России?Готовы ли вы предложить что-то иностранному заказчику?
- Нашими постоянными заказчиками являются ведущие производственные предприятия России, Украины и Белоруссии, работающие в электроэнергетике, аэрокосмическом секторе, судо- и машиностроении и других ведущих отраслях промышленности. С европейскими компаниями трудно конкурировать по причине того, что уровень развития технологий у них на порядок выше российских. С модернизированным оборудованием на европейский рынок бессмысленно идти, потому что там есть свои компании, которые в состоянии это делать, тем более, что при модернизации оборудования мы используем западные технологии и западную компонентную базу.
- Новые технологии в станкостроении: много ли инноваций применяется в этой сфере?
-Станкостроение, пожалуй, больше чем многие другие отрасли потребляет и создает инновации. Ключ к успеху – грамотное применение современных технологий при производстве станков. Это увеличивает стоимость оборудования, расширяя его возможности и повышая уровень качества производимой продукции. Станкостроение – одна из самых наукоемких отраслей машиностроения. Производство средств производства требует на порядок более квалифицированной конструкторской и технологической подготовки, поэтому станкостроение является технологическим базисом любого государства, претендующего на техническую и технологическую независимость.
- Известно, что «Киров-Станкомаш» был инициатором создания Кластера станкоинструментальной промышленности Санкт-Петербурга. Расскажите, пожалуйста, об этом подробнее.
- Созданный на базе и при поддержке Кировского завода региональный станкоинструментальный кластер в статусе некоммерческого партнерства объединил практически всех производителей станкоинструментального оборудования Северо-Запада России. Все его16-ть участников поставили своей целью обеспечение жизненного цикла (НИОКР – постановка на производство – серийный выпуск) инновационного, наукоемкого оборудования и технологических услуг для ведущих отраслей экономики и промышленности России. Все условия для этого в нашем регионе есть. Исторически так сложилось, что в Санкт-Петербурге изначально был ряд заводов, которые специализировались на производстве станочного оборудования и компонентной базы для станков, а также предприятий, которые занимались разработкой и поставкой измерительного и гидравлического оборудования, программного обеспечения и т.п.
Другой вопрос, что продукт должен быть обеспечен спросом, и мы сейчас активно продвигаем наши совместные проекты на различных уровнях. Необходимо здесь и участие государственной власти в виде финансовой и политической поддержки проектов развития станкостроения. Нам необходимо принять единую политику и действовать консолидированно для повышения конкурентоспособности отечественных производителей. Поодиночке трудно противостоять огромной массе импортного оборудования, которая хлынула на российский рынок. Никакие заградительные пошлины не могут помочь, потому что спрос превышает предложение в разы: объем рынка металлорежущего оборудования оценивается примерно в 50 миллиардов рублей, при этом отечественные предприятия производят продукции в лучшем случае на 1,5-2 миллиарда рублей. Недостающее предложение, естественно, замещается импортным товаром. Уже сегодня в Россию завозится в трис лишнимраза больше оборудования, чем производится внутри страны.
- Какой вклад в решение этой задачи собираетесь сделать Вы?
- Наша компания позиционирует себя в качестве инжиниринговой компании, сейчас мы твердо обосновались в этой нише и, думаю, мы сделали правильный выбор направления деятельности, предоставляя заказчику полный спектр работ. В перспективе мы будем усиливать свои технологические компетенции, расширять номенклатуру станочной продукции и развивать сервис. Сегодня мы также находимся на стадии опытных конструкторских работ по зубообрабатывающим станкам нового поколения. Надеюсь, нам удастся реализовать наши задумки и выйти на рынок с новым отечественным продуктом. Быть ближе к заказчику и стать его партнером – наша основная цель. Мы намерены кратно увеличить свою выручку - к 2015 году выйти на уровень не менее 3 млрд рублей, для сравнения сейчас наша выручка составляет не более 400 млн рублей.
Новости компаний 30.01.2025
Новости компаний 27.11.2024
Новости компаний 11.09.2024
Новости компаний 08.08.2024
Животноводство 05.02.2025
Животноводство 27.01.2025
Животноводство 10.10.2024
Животноводство 18.11.2021
Животноводство 17.05.2021
Чтобы оставить комментарий или выставить рейтинг, нужно Войти или Зарегистрироваться
Читайте также