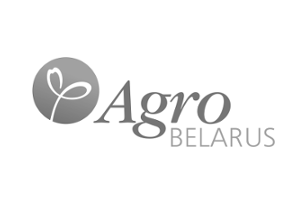
Бытовая химия: как выбрать и где купить в Беларуси
09.03.2025
Мы занялись этой темой. К концу 2003г была создана небольшая экспериментальная установка с целью разработки, как самой конструкции будущих линий, так и технологии. Исходили из технологической задачи утилизации отходов, состоящей в том, чтобы птицефабрика использовала исключительно свое сырье, т.е. б/у прокладку и яичный гофроящик.
2. Технологическая задача. Главная проблема заключалась в том, что во всей научно-технической литературе и по практике производства сложных литых изделий путем вакуумной формовки, а именно бугорчатая прокладка является таким изделием, применяется только качественное сырье с добавлением целлюлозы и различных клеев. Качественным сырьем является целлюлоза и первичная макулатура. А б/у прокладка является вторичной макулатурой и как сырье при производстве литых изделий вакуумной формовки не годится. Б/у прокладку загрязненную меланжем и в макулатуру сложно сдать, ее принимают с большими сложностями.
В процессе вторичной переработки макулатуры целлюлоза теряет свои физико-химические свойства: ворсинки целлюлозы дробятся, ораговевают, теряют смачиваемость, эластичность и сцепляемость. Прокладка как изделие имеет очень сложную конфигурацию. При передаче в формовочном станке мокрой сформированной прокладки с матрицы на пуансон она рвется или не передается из-за того, что сделана из «некачественного сырья». Ворсинки целлюлозы не сцепляются прочно, и она попросту разваливается - не является целым изделием.
Различные производители прокладки под яйцо, а это в основном целлюлозно-бумажные комбинаты (ЦБК), применяют в сырье «древесную массу» - целлюлозу 60% и более. Макулатура у них идет как добавка. В России до 2003г было несколько мелких производителей прокладки, которые работают еще с советских времен только на первичной макулатуре с добавлением различных клеев. Также в России уже были производители такого оборудования, у них в технологии тоже не было применение б/у прокладки – только первичная макулатура и различные клеи.
Таким образом, мы приступили к выполнению нашей задачи понимая, что невозможно использовать в сырье б/у прокладку. Но, у птицефабрики есть возврат тары, есть изношенная загрязненная прокладка и ее надо утилизировать! И утилизировать надо с выгодой для птицефабрики! Необходимо изобрести такую технологию и оборудование, которые выполняли бы эту задачу.
3. Разработка оборудования и опробование технологии. В свое время, для одной бройлерной птицефабрики Луганской области я искал возможность добавления в комбикорм
В результате многомесячных проб вышли на сырьевой состав, где: б/у прокладка 50%, гофрокартон 20% и макулатура (газетная и архивная) 30%, и определенный состав клея на основе лигносульфоната. С таким соотношением сырья и разработанными конструктивами различных по производительности линиями обратились в конце 2003г к генеральному директору СООО АВИС Серебрякову Александру Сергеевичу (Луганская птицефабрика). Совместно была определена производственная линия с производительностью до 450000шт/мес при 3х сменном режиме, 30раб.дней. Наше название линии - комплекс «Сурмач КС720».
4. Производство и пуск комплекса «Сурмач КС720». В феврале 2004г определились с помещением под цех прокладки. Была выбрана часть птичника (полурамника) длинной 25м. Выстроили внутри птичника перегородку из шлакоблока, за перегородкой сидела птица. Конфигурацию размещения линии провели исходя из возможности помещения 18мх25м. Оборудование производили блоками на мех.заводе, сборку и покраску провели на месте. Комплектация линии - с резервными агрегатами. Все агрегаты украинского производства, включая пневматику «Camozzi» Симферопольского завода. С Александром Сергеевичем договорились о первоочередном производстве и запуске производственной линии, а после опробования приступить к производству линии сушки. Ко дню праздника «Великой Пасхи» произвели первую пробную партию прокладки. За апрель-май была смонтирована камера сушки с 9ю контейнерами.
Итак, конфигурация цеха линии КС720 состояла из: склада сырья; компрессорной; комнаты приготовления хим.растворов; узла гидроразбивателя; блока баков под воду и бумажной массы: 5% и 1%; мусороулавливателя; рабочего бака пульпы; формовочного станка на две матрицы с программным обеспечением; блоков насосных агрегатов параллельно с резервными; блока вакуумного водоотделителя с двумя вакуумнасосами; камеры сушки с газовым теплогенератором и 9ю контейнерами; суточного склада готовой прокладки из расчета не менее 15000 шт.
Проведенные рабочие испытания утвердили технологию по сырью: 70% б/у прокладка, 30% макулатура и хим.растворы лигносульфонатных клеев и парафиновых эмульсий. Такое соотношение фабрику устраивало, и в июне к работе приступила первая смена рабочего персонала. В смену вошли 3женщины и 1слесарь, также был назначен начальник цеха – бывший бригадир птицеводческой бригады. Начальнику цеха была поручена задача набора персонала на 2ю и 3ю смены и выход на производственную мощность.
1. Совершенствование технологии и схемы менеджмента цеха. В конце 2005г цех работал в 2 смены с производительностью на 50%. На 3ю смену так и не смогли набрать людей. Состав сырья не изменялся. Я предложил руководству изменить ситуацию по цеху с персоналом и опробовать новую технологию, где в сырье пойдет 100% б/у прокладка. Спасибо Александру Сергеевичу, что он подошел конструктивно к решению проблем цеха. Была произведена замена начальника цеха и практически всего рабочего персонала, цех был снят с минимальной зарплаты и был поставлен на разработанную систему оплаты от произведенного количества прокладки. По оборудованию пришлось произвести ремонт в январе 2006г, а с февраля цех начал работать в одну смену. Проводили в рабочем режиме подбор персонала на 2ю смену, и с начала марта цех работал уже в две смены.
После нескольких испытаний, разработки нового программного обеспечения и переделки формовочного станка начали применять новую технологию. Теперь в сырье шла 100% своя и привозимая из других фабрик (оптовиков, рынка) б/у прокладка с добавлением яичного гофроящика. Клей уже не применялся. В комнате приготовления хим.растворов поставили мельницу по размолу гофроящика обмотанного скотчем и сильно загрязненной яичным меланжем прокладки. Применение разработанной оригинальной конструкции мельницы позволило перемалывать сырье с большими включениями засохшего меланжа, скорлупы, скотча, веревок, тряпок и другого мусора, имеющегося с избытком в прокладке и гофроящике. Металлические включения выбираются магнитом, твердые – выводятся под собственным весом в конструктивный «карман» при прохождении выдувного сопла мельницы.
Таким образом, отходов больше не было, все отходы по таре шли в сырье.
2. Производство прокладки птицефабрикой из своего сырья. На производственную мощность в смену заявленную нами в паспорте: 720 шт/ч х 0,8 (коэффициент рабочего времени) х 8раб.ч = 4600 шт/см цех вышел в работе на две смены. На три рабочих смены цех не смог выйти из-за двух причин. Во-первых, давление газа составляло 1,8-2,2кПа, а зимой опускалось до 0,7кПа, это вместо заявленных мин. 3кПа. И прокладка просто не успевала высыхать, вместо 45мин партия из 4х контейнеров сохла за 2-3часа. Летом высыхала за 1час. Во-вторых, рабочий цикл формовки с паспортных 10сек был нами увеличен до 13сек, хотя этот фактор не являлся задерживающим как сушка, а у некоторых операторов цикл уменьшался до 7-8сек (время цикла выставляется в программе формовочного станка оператором). Здесь уже включался опыт и профессионализм оператора.
Так как давление и качество газа невозможно было поднять и к тому же руководство фабрики поставило план всего 150000 шт/мес, цех так и работал в две смены с полными выходными, выпуская прокладки 150000-190000 шт/мес. Были случаи, что пытаясь заработать денег цех фактически увеличивал производительность почти в 2 раза от паспортной, например за январь 2007г цех выпустил 237000 шт за 14 рабочих дней. Потребности самой фабрики были порядка 100000-120000 шт/мес, излишки продавались другим птицефабрикам.
В процессе наработки опыта персоналом начальник цеха сократил персонал от положенного по штату в 2раза и рабочие часы были по графику удобному работникам. 1я смена начиналась с 8.00 утра, выходили нач.цеха и две женщины-операторы (женщины отводили детей в школу поселка на 7.30). До 12.00 производилась вся сменная норма прокладки (мы добавили еще 5 контейнеров), часть прокладки до 12,00 высыхала. После женщины-операторы уходили (в школу за детьми и домой), а к 12.00 приходил слесарь 1й смены. Слесарь сушил произведенную прокладку, чистил оборудование, проводил регламентные мероприятия (именно это не привело ни разу к аварийной остановке) и еще делал самостоятельно несколько контейнеров прокладки. В 20,00 приходила 2я смена: две женщины-оператора и слесарь. Женщины работали до 6,30 и уезжали на фабричном автобусе, а слесарь сдавал смену в 8,00. Зарплату получали на цех, в зависимости от сданной прокладки за месяц. Попасть на работу в цех прокладки было престижно.
Была отработана специальная программа начисления заработной платы на каждого работника цеха в зависимости от объема конечного выпуска прокладки, изменения цен на энергоносители и воду, должности, выходов и т.д. В программу вводились каждый месяц новые цены, себестоимость увеличивалась, но персоналу зарплата начислялась фиксированной формулой, где вычитались затраты на энергоносители и воду. Это заставляло персонал или увеличить выпуск прокладки или уменьшить штат цеха. Кроме того ежемесячно начислялся и фонд цеха из денег выделенных на персонал. Фонд цеха был направлен на расходные материалы и ремонт оборудования, что заставляло всех работников относиться максимально бережно к оборудованию, т.к. излишки фонда в определенные периоды распределялись в виде премий.
Данная система менеджмента привела к самостоятельности цеха. Руководство птицефабрики не касалось работы цеха, ремонт оборудования проводился самим цехом и за счет фонда цеха. Все работники цеха были в штате фабрики, но графики выходов, отпусков и все другие вопросы решались только внутри цеха. Вопросы погрузки и привоза сырья с тарного склада, отгрузка готовой прокладки по птичникам и яйцесклад и т.д. решал начальник цеха самостоятельно. Директор птицефабрики встречался с начальником цеха практически раз в месяц по отчету сданной прокладки за прошедший месяц.
Зимой 2007г, после новогодних праздников, произошло «зависание яйца» на рынке. Прокладка не возвращалась с рынка и сырья не стало. Возникла необходимость закупки макулатуры, что привело бы к увеличению себестоимости прокладки. Коллектив цеха проблему решил по своему: начали разбирать старый тарный склад еще с советских времен. Практически до середины мая работали на прелом грязном сырье. В этот период возобновили применение лигносульфонатного клея. Закупленные в спешке 3т макулатуры распределили на полгода. Именно в этот период наша технология абсолютно доказала возможность производства прокладки птицефабрикой из своего сырья, каким бы мусором оно не являлось.
1. Закрытие цеха прокладки на СООО АВИС. Как нам всем известно, в яичной отрасли 2007г обозначился началом кризиса. На АВИСе к этому времени некоторые птичники перешли на современное клеточное 5ти ярусное оборудование и некоторые готовились. Корпус, в котором находился цех прокладки, также должен был стать частью современного комплекса из 4х птичников и яйцесклада с единой системой транспортировки яйца на фасовку. Проект предполагал комплекс из 4х соединенных птичников, яйцесклада с фасовкой яйца и цеха производства прокладки, где приемка сырья (б/у прокладки) была бы уже за забором птицефабрики. Схема цеха прокладки: прием возвратной тары в тарный склад за забором птицефабрики; в складе отгружается загрязненная б/у прокладка и рваный гофроящик; сырье транспортируется в блок «массоподготовки» цеха, который уже на территории фабрики; все сырье перерабатывается и производится новая прокладка; прокладка проходит сушку в камере при 1200С; упаковывается в пачки и складируется в цеховом суточном складе; транспортируется в яйцесклад и в птичники на фасовку яйца. Т.е. яйцо фасуется в прокладку, которая не была за забором птицефабрики!
Цех прокладки работал до 1го сентября 2007г, все клеточное и вентиляционное оборудование еще с июля лежало у птичника, необходимо было срочно закрыть производство прокладки, демонтировать оборудование и начать подготовку корпуса к монтажу клетки.
За две недели линия КС720 была разобрана и вывезена: блоки баков, камера сушки с контейнерами, трубопроводы, вакуумный водоотделитель были отвезены на место будущего цеха возле строящегося яйцесклада. Насосы, гидроразбиватель и формовочный станок в слесарную мастерскую. Но, кризис разрастался и этим планам не суждено было сбыться до сих пор.
2. Полученный в результате работы цеха вывод. Мы создали такую технологию, т.е. реальное поточное производство прокладки исключительно из сырья птицефабрики. На Луганской птицефабрике был создан «Цех прокладки», нами была спроектирована и произведена линия «КС720». За время практической работы цеха была отработана эффективная система менеджмента производства с расчетом на сельский персонал. Результат:
- поточное производство прокладки внутри птицефабрики, поставки прокладки из цеха прямо в птичники и яйцесклад, т.е. перемещение только внутри фабрики;
- в сырье идет 100% возвратная тара - загрязненная прокладка, клей использовали только при прелом сырье;
- по экономике: себестоимость в 2004-2007г.г. варьировалась от 12 до 17 коп/шт при закупочной цене в 20 – 27 коп/шт. По расчету в 2009г. 22 - 27 коп/шт при закупочной цене в 34 – 43 коп/шт. Кроме того нет затрат на сжигание или вывоз на полигон. А еще есть прибыль от продажи излишков другим птицефабрикам по области;
- полученная прокладка гораздо прочнее, вершины не сминаются, исключен бой в транспорте, стали делать полную до крыши загрузку в «бычках» и «ГАЗелях»;
- в январе 2005г. наша прокладка прошла пробу сотрудниками фирмы «Авангард» на упаковочной линии «МОВА» на птицефабрике в г.Ивано-Франковске. Результат в сравнении с другой прокладкой – ни одного сбоя! Наша прокладка свободно выходила из пачек и загруженная яйцом не срывалась с захватов;
- наше оборудование технически простое, спроектировано с расчетом на сельский персонал, что является основополагающим фактором при освоении производства на птицефабрике!
Таким образом, произведенные нами технология и оборудование опробованы в реальных условиях птицефабрики. Производство птицефабрикой прокладки под яйцо из 100% своего сырья это реальность. И очевидна выгодность собственного производства птицефабрикой прокладки, особенно после возможного введения в будущем требования о строго-одноразовом использовании прокладки без ее использования вторично - ведь в странах СЭС по EN ISO 9001 бугорчатая прокладка под яйцо является одноразовой.
Разработанные нами конструктив и программное обеспечение полуавтоматического формовочного станка; обычные и простые в обслуживании агрегаты; доступная по цене и обслуживанию пневматика; простота самой технологии производства, где нет необходимости проводить различные степени очистки и поддержания точной концентрации бумажной массы; ежедневный контроль качества при сдаче прокладки на фасовку яйца; санитарные нормы; система оплаты и другие наработанные факторы явственно свидетельствуют о правильности освоения птицефабриками в будущем своего производства прокладки.
Кроме прокладки на данном оборудовании фабрика может зарабатывать деньги на производстве другой продукции, например на производстве торфяных стаканчиков под рассаду. По расчетам 2011г. себестоимость производства торфяных стаканчиков популярных размеров 60х60 и 80х80 варьируется в пределах 7-10коп/шт - это при оптовой цене в пределах 30-60коп/шт.
3. Вид оборудования. Практика работы комплекса КС720 на СООО АВИС показала, что основная проблема, как производительности, так и работоспособности комплекса заключается в рабочем персонале. Мы пришли к тому, что если внедрять на птицефабрике что-то новое, то только на основе схемы самоокупаемости.
Мы определили и практически отработали такую схему. Наша практика показала, что все зависит от персонала и максимальный эффект дает именно данная схема организации производства. Основной принцип данной схемы заключается в том, что фабрика, образно говоря «покупает» по фиксированной цене прокладку у цеха (принцип описан выше). Таким образом, в цехе слаживается самостоятельный коллектив, а фабрика, утилизируя свои отходы, получает прокладку на 50% дешевле от рыночной стоимости. Излишки произведенной прокладки фабрика продает по своему региону.
ВАЖНО: Из практики реального производства прокладки доказано:
1) с использованием в качестве сырья 100% б/у прокладки (т.е. того сырья, которое есть у птицефабрики) автоматические линии не работают. Данный факт можно легко проверить, связавшись с производителями подобных производственных линий, изучив технологическую литературу переработки макулатуры, или обратившись к технологам предприятий производства прокладки. Автоматические линии работают только на хорошем сырье, т.е. на первичной макулатуре или качественном – с добавлением целлюлозы, а для птицефабрик выгодно утилизировать собственные отходы (б/у прокладку и гофроящик, очень загрязненные меланжем и скотчем) вместо закупки дорогостоящего макулатурного сырья.
2) имеющийся профессиональный и психологический уровень сельского персонала, т.е. реально имеющихся рабочих ресурсов на птицефабрике, и имеющегося сырья позволяет организовать эффективное производство прокладки именно на полуавтоматических формовочных станках, т.е. на наших линиях «Сурмач720» или «Сурмач1440» со «специальным программным управлением параметров формовки».
Отработка оборудования и технологии в реальных условиях работы на птицефабрике доказала правильность именно «программно-станочной» схемы полуавтоматических линий производства прокладки – это оборудование именно для птицефабрик.
Мы проводили разработку комплексов на производительность 1440 и 2880 шт/ч с роботом автоподпрессовки прокладки, выпускаемая прокладка будет абсолютно подходить под упаковочно-сортировочные линии типа ARDENTA__R фирмы «Staalkat» или других з ападных фирм. Данный робот монтируется в зоне камеры транспортерной сушки комплекса «Сурмач1440 и 2880».
Технико-расходные характеристики установок «Сурмач»
Параметр |
Сурмач-720 |
Сурмач-1440 |
Производительность (шт./час) |
720 |
1440 |
Число рабочих в смене |
4 |
5 |
Расход макулатуры МС1, 2, кг/час (30%) |
15 |
30 |
Расход б/у ячейки, кг/час (70%) |
35 |
70 |
*Расход б/у ячейки и/или б/у гофрокартона при 100% в сырье |
60 |
120 |
Расход воды, л/час |
60 |
120 |
Расход газа, м3/ч |
16 |
40 |
Потреб. эл.энергии, кВт/ч |
55 |
100 |
Количество станков |
1 |
2 |
* при нашей технологии, где в сырье идет 100% б/у ячейки или б/у гофрокартона. При этом прокладка может иметь повышенную массу до 85гр.
Расчет реального производства:
На установку «Сурмач 1440» добавляется один оператор формовочного станка на смену. Схемы размещения установок 720 и 1440 с минимальными габаритными размерами помещений даны ниже.
На производство «бугорчатой прокладки под яйцо» национального ДСТУ не существует, т.е. необходима разработка собственных ТУ на производство. Но при производстве для своих целей ТУ не разрабатывается, а также, если продукция производится согласно техническому заданию, утвержденному между двумя предприятиями, т.е. производителем и потребителем (см. «Правила погодження та прийняття ТУ» ДСТУ 1.3:2004).
Процесс производства комплекса может происходить двумя способами:
- производство и монтаж всего комплекса в г. Луганске, его запуск и проверка работоспособности, а затем демонтаж, перевозка на место, монтаж и пуск с обучением персонала (срок в общей сложности 6-7мес);
- производство и монтаж всего комплекса на месте с обучением персонала (срок 4-5мес). В этом случае основные узлы (формовочный станок, гидроразбиватель, деталировка и узловая сборка, электрошкафы и электроника) производятся у нас, а затем перевозятся и монтируются с остальной частью в комплекс на месте.
Цены оговариваются в каждом случае отдельно, но однозначно не выше типового оборудования российского производства. При заказе птицефабрики и на другие наши виды оборудования (тензовесы или линии по концентратам) цены будут снижены.
Пресс-формы мы заказываем у наших партнеров в России. Качество пресс-форм определяется точной конфигурацией, которая обеспечивается высокоточной фрезеровкой изготовляемых ламелей. Пресс-формы изготавливаются из высокопрочных материалов: латуни, алюминия, нержавеющей стали, композитных материалов. Типоразмеры:
При возникшем интересе к оборудованию производства прокладки и упаковочных изделий из макулатуры или торфяных стаканчиков можно связаться со мной по телефону и E-mail. Охотно отвечу на интересующие вопросы, также могу предоставить видео работы цеха.
Анатолий Криеренко
ptichki.net
Новости компаний 13.11.2023
Новости компаний 07.12.2022
Новости компаний 13.01.2021
Новости компаний 18.08.2020
Новости компаний 19.06.2020
Животноводство 05.02.2025
Животноводство 27.01.2025
Животноводство 10.10.2024
Животноводство 18.11.2021
Животноводство 17.05.2021
Чтобы оставить комментарий или выставить рейтинг, нужно Войти или Зарегистрироваться